Efficient continuous improvement is more approachable than you may think. Despite technology advancement, some basic tools supporting business growth have not changed. Although all of them were developed decades ago, their relevance remained unchanged.
1. Check sheet
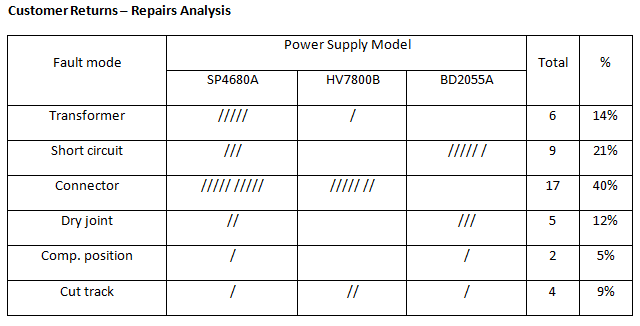
- Studies causes of problems
- Also known as Tally Sheet or Tally Chart
- Measures frequency of occurrence
- Presents analysis immediately
- Collect data on demand for products and services
2. Control chart
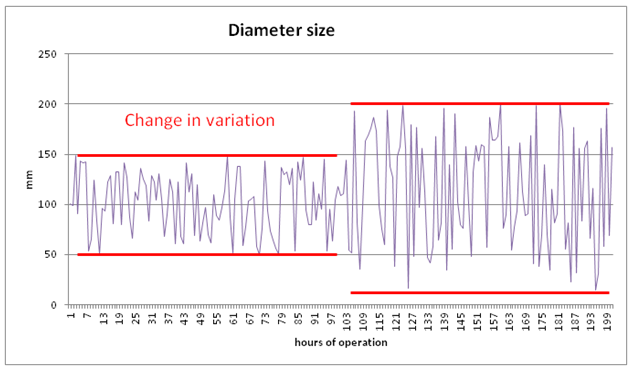
- A special type of Run Chart
- Control limits highlight changes beyond expected results
- Time series plots show measured values plotted against time
- Indicates trends, cycling behaviours
- Finds opportunities for elimination of special causes
3. Pareto chart
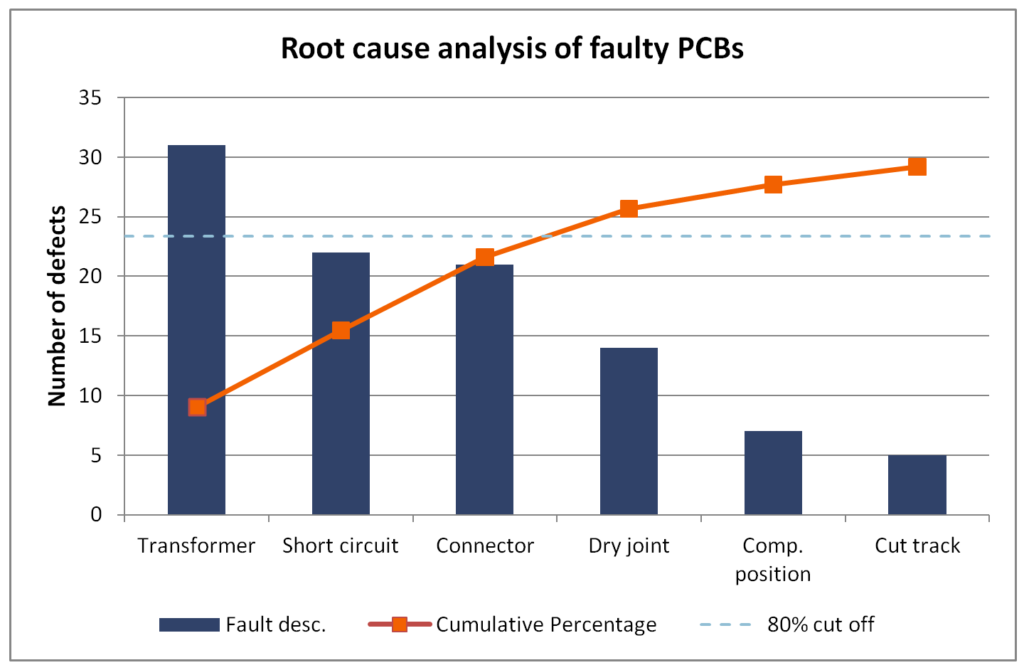
- 80/20 rule – 80% of problems are related to 20% of causes
- Four different points of reference:
- Quantity (frequency)
- Cost
- Time
- Severity
- Before you start:
- Relevant data has been collected
- The scope of the study has been agreed
Download your FREE copy of PARETO TEMPLATE from the PREMIUM LIBRARY
4. Cause and Effect Diagram
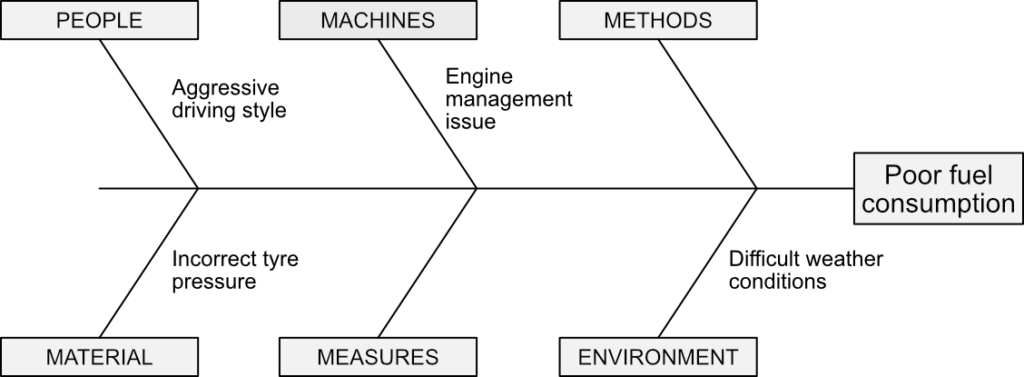
- Also known as the Ishikawa diagram or “fishbone” diagram
- Used to brainstorm possible causes of a problem
- Focuses on the root cause, not the symptoms of a problem
- “6Ms” – men/people, machines, methods, materials, measures, mother nature/environment
- “4Ps” (for service operations) – places, procedures, people, policies
5. Scatter Diagram

- Also known as correlation chart or scatter plot
- Presents the relationship between two variables
- Type of correlation
- Strength of correlation
- Changes to the independent variable may drive changes to the dependent variable
6. Flow Chart
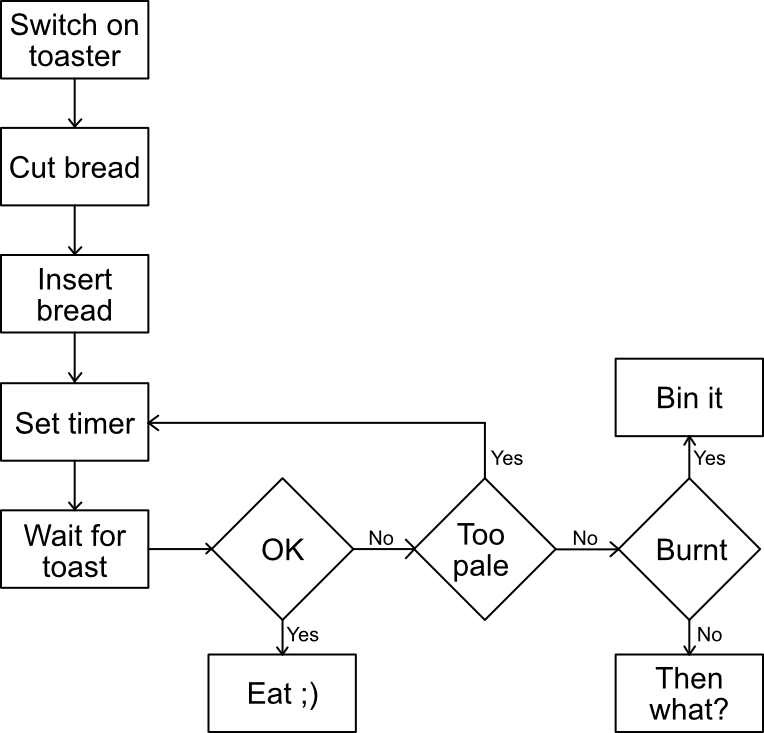
Sequence of steps in processes- Identifies relationships in processes
- Highlights potential bottlenecks and deficiencies
- Identifies feedback loops and critical steps
7. Histogram

- Graphical representation of data distribution
- Plots quantitative data
- Shows variability of the process
- Indicates process performance based on sample information
2 Comments
Leave your reply.